Metal Shear
Jiangyin Aupu Machinery Co.,Ltd.:Your Trustworthy Metal Shear Manufacturer!
Our company is a professional design and manufacture company of hydraulic machinery. We are a backbone company in manufacturing all kinds of hydraulic equipment and metal machineries in domestic. Our company has been through professional quality system certification, CE certification, SGS audit and as a member of the China national resources recycling association.
Leading Service
We are committed to constantly innovating our products to provide foreign customers with a large number of high-quality products to exceed customer satisfaction. We can also provide customized services according to customers' requirements such as size, color, appearance, etc. We can provide the most favorable price and high-quality products.
Quality Guaranteed
We have been continuously researching and innovating to meet the needs of different customers. At the same time, we always adhere to strict quality control to ensure that the quality of every product meets international standards.
Wide Sales Countries
Our products have been exported to more than 40 countries, such as Russia, Australia, USA, UK, Germany, Ukraine, Iran, Romania, Hungary, Mexico, Brazil, Chile, Canada, Spain, Colombia, etc. We have agents in the USA, Australia, Singapore, Kuwait, Russia.
Various Types of Products
Our products have 13 series, a total of more than one hundred varieties, including Y81 series hydraulic metal baling machine, Y82 series non-metal hydraulic baling machine, Y82 series scrap tire baling machine, Y83 series hydraulic scrap briquetting press, HBS series large shearing baler, Q43 series crocodile hydraulic shears, Q15 series gantry plate shears, Y32 series four-column hydraulic press, EPM series automatic waste paper baler, KSB series waste shredder and so on.
-
Hot Sale Heavy Duty Scrap Metal Hydraulic Shear BalersFeatures HBS series heavy duty steel shear, used in all kinds of thin material the production and life use scrap steel and light metal structure all kinds of plastic non-ferrous metal (stainless steel steel etc.) after the compression packaging directly cut into required sizeread more
-
Good Quality Hydraulic Waste Metal Steel Shear Baler MachineHBS Scrap baler shear machine, This equipment mainly can be used to: pre compression and shear waste.Shear reinforcement steel.Pack light.Compression, shear car bodies.Shear packer HDJ series heavy-duty hydraulic shearing machine, used for various thin material, the production and living with...read more
-
Hydraulic Heavy Duty Scrap Baling ShearOur balers have 13 series,including Y81 series hydraulic metal baling machine, Y82 series non-metal hydraulic baling machine, Y82 series scrap tire baling machine, HBS series large shearing baler,Q15 series gantry plate shears, Y32 series four-column hydraulic press, EPM series automatic waste paper baler, KSB series waste shredder and so on.read more
-
Box Shear BalerBox shearing machine is a method commonly used in scrap steel processing and production. It is widely used in the field of scrap steel processing and is one of the main methods for scrap steel processing.Compared with flame cutting, equipment shearing has the advantages of high degree of mechanization, high operation efficiency, low scrap steel loss, and no air pollution...read more
-
Automatic Horizontal Shear MachineThe fully automatic shearing machine is mainly used to cut the straight edge of metal sheets of various sizes, and is widely used in various industrial sectors such as steel rolling, automobiles, airplanes, ships, tractors, bridges, electrical appliances, instruments, boilers, etc...read more
-
High Pressure Hydraulic Scrap Metal Plate guillotine Shearing MachineHydraulic Scrap Metal Plate Guillotine Shearing Machine is a type of equipment used for cutting and processing scrap metal plates. It is widely used in the metal recycling industry and can be used to process various types of metal plates, such as steel plates, aluminum plates, copper plates, and so on...read more
-
Hot Sale Scrap Metal Guillotine Shear MachineQ43 series Corcodile shear machine This machine is used for a variety of cross-section shapes such as round steel, square steel, Angle steel, i-steel, plate steel, steel pipe, such as waste of cold shear, hot rolled small scale cut steel, steel rolling mills scale cutting, etc The properties and...read more
-
Hydraulic Heavy-Duty Shear for factory direct saleMetal Shear, Metal Baler, Scrap Metal Baler manufacturer / supplier in China, offering Hydraulic Heavy-Duty Scrap Baling Shear and so on.read more
-
Heavy-Duty scrap hydraulic shearing machineBaling Shear, Shear Baler, Shear manufacturer / supplier in China, offering Heavy-Duty Scrap Shears, Waste Paper Vertical Baler, and so on.Scrap recycling machine, to smelting, you can have many choices here.10 years manufacture experience.read more
-
Guillotine Shear for metal materials cuttingShears, Guillotine Shears, Hydraulic Shears manufacturer / supplier in China, offering Hydraulic Guillotine Shears Machine, CNC / Nc, Hydraulic Shearing Cutting Machine, Plate Shearing Machine, Hydraulic Swing Beam Shearing Machine, Hydraulic Swing Beam Shearing Machine and so on.read more
-
Automatic Gantry ShearQ91Y Series Automatic Gantry Shear For all kinds of production and life use scrap non-ferrous metal (stainless steel, copper, etc.) directly cut into the required size.read more
-
Good Quality Double-edged Crocodile-type Hydraulic Shearing MachineQ43 series Corcodile shear machine Q43 series crocodile type metal shear is suitable to shear various sharps of profiled bar and varieties of metal structure parts at cold condition for metal recovery companies, waste steel works, smelting and casting enterprises. PRODUCT FEATURES: 1.Hydraulic...read more
A Metal Shear is an industrial machinery with rotating disks and blades to cut metal bars and hard iron sheets. Shearing refers to applying high pressure on a metal bar once to remove a portion of the metal. The cutting mechanism of all metal shears uses the same arrangement of a fixed upper blade, a lower blade, and an adjustable clearance between the two. When pressure is applied to the upper blade, the lower blade is compelled to cut and split the metal in two.
Benefits of Metal Shear
Precision Cutting
Metal Shears are integral to the steel rolling mill industry due to their unparalleled precision in cutting steel products. In an industry where the quality of the final product is essential, the ability to make clean, precise cuts is indispensable. These machines excel in providing accurate cuts, ensuring that the steel products meet the required specifications.
Enhancing Productivity
Efficiency is the linchpin of any steel rolling mill. Metal Shears significantly enhance productivity by cutting steel at predetermined lengths swiftly and accurately. This saves time and reduces material wastage, making your operations more cost-effective.
Safety and Operator Convenience
Metal Shears come equipped with safety features that protect operators from potential hazards. These features often include safety covers, emergency stop buttons, and other safety mechanisms. Moreover, modern machines boast user-friendly interfaces, making them easier for operators to control and monitor, further enhancing safety. The semiotics design of our machinery intuitively induce safety.
Reducing Downtime
Regular maintenance of Metal Shears can prevent unexpected breakdowns and downtime, ensuring that your rolling mill operates seamlessly. By following the right maintenance procedures, you can extend the lifespan of your machines and maximize their efficiency, effectively minimizing costly interruptions.
Types of Metal Shear
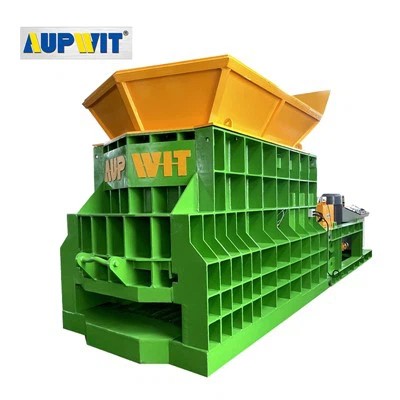
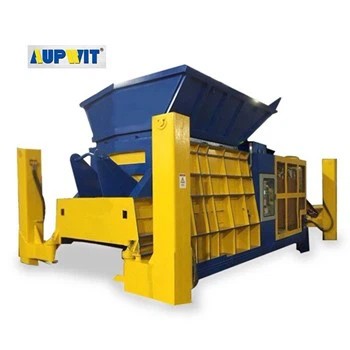
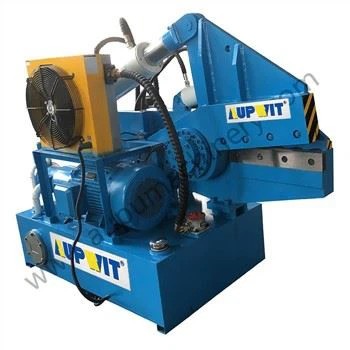
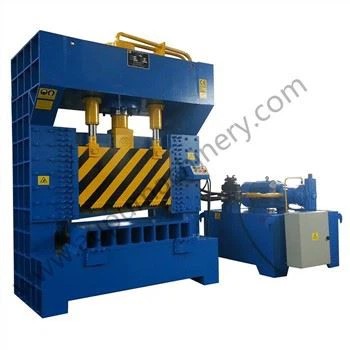
Alligator shear
So-called because of the hinged jaw used to cut metal, alligator shears are powered by a hydraulic cylinder and are mostly used for cutting long metal stock like l-beams, angle iron, pipe or rebar, or to prepare scrap metal for shredding by lopping off anything the shredder will not accept or non-metal fittings. The cutting motion is actuated by a piston which extends to slowly close the upper ‘jaw’ down alongside the bed. The key strengths of an alligator shear are its cost-effectiveness, strength and durability, it’s drawbacks are its inaccuracy and rough finish.
Metal guillotine
Guillotines consist of a shear table, work-holding device, a gauging device and upper and lower shears. It can be mechanically, hydraulically, or foot-powered and works by clamping the metal with a ram, then moving a metal blade down across a fixed blade to make a cut. The moving blade can either be straight or set on an angle, to decrease the amount of force required to cut a larger piece of metal.
The key strengths of working with a metal guillotine include its speed and cost-effectiveness, which is ideal for high volume production. However, the biggest drawback of a metal guillotine is its tendency to produce a rough edge. These machines are ideal for process parts where aesthetics are not important, or where the metal will go on to be further worked through welding. Always ensure you are employing correct safety measures when operating a guillotine.
Bench shear
A bench mounted shear that offers more mechanical advantage through a compound mechanism, bench shears are ideal for cutting rough shapes from medium-sized pieces of sheet metal. A dynamic piece of machinery, the bench shear can be used for a number of different purposes including 90-degree angle cuts and T-sections as well as cutting both round and square bars.
The strength of a bench shear depends on its size, with larger machines capable of withstanding the highest stresses, but broadly speaking, the key strengths of this type of shearing mechanism are its efficiency and ability to produce a clean cut that’s free of burrs.
Power shears
Ideal for blanking large pieces of sheet metal, power shears are either electrically or pneumatically powered and operated by hand. They work with an upper blade moving towards a lower fixed blade and exerting tension on the cutting material. They are generally used for cutting straight lines or large radius curves.
The key advantages of power shears are their flexibility in cutting curves, efficiency, accuracy, durability and quality finish.
Throatless shear
Perfect for making straight, intricately curved or irregular cuts, the throatless shear differs from the other models on this list because its design allows for the cutting material to be freely moved around.
Snips
Snips are hand tools used to cut sheet metal. There are two different types of snips: tinner snips and compound action snips. Tin snips have long handles and short blades, and are generally used to cut low-carbon tin or mild steel. Straight pattern tin snips are ideal for cutting straight lines or gentle curves, whilst duckbill pattern tin snips are ideal for cutting sharper curves. There are also tin snips known as circle pattern, which cut circles, hawksbill pattern which cut radii on the inside and outside of circles as well as cuts which require sharp turns like when cutting holes in pipes.
The other type of snip is the compound action snip, which is used to cut aluminium, mild steel or stainless steel. This type of snip has a linkage, which increases mechanical advantages. Compound action snips come in three different types:
Straight-cutting (which cut straight and in a wide curve)
Left-cutting (which cut straight and in a tight curve to the left)
Right-cutting (which cut straight and in a tight curve to the right)
Nibblers
Although some nibblers work like tin snips, most work off a punch and die formation. Nibblers work via a blade which moves in a line around a fixed die in a series of up and down punching strokes, ‘nibbling’ away at the material to create a cut.
The advantages of nibblers include their robustness and durability, its ability to produce distortion-free cuts, speed, and low force feed.
How to Maintain Metal Shear
Lubrication
Proper lubrication is the lifeblood of your Metal Shear. It prevents excessive friction, wear, and tear on moving parts. Regularly inspect and lubricate the bearings, gears, and other critical components according to the manufacturer’s recommendations. Using the correct type and amount of lubricant is crucial for optimal performance, as insufficient lubrication can result in premature wear and decreased efficiency.
Blade Maintenance
Blades are the heart of a Metal Shear, and their condition directly affects the quality of the cuts. Periodically inspect the blades for wear, nicks, or damage. If you notice any issues, sharpen or replace the blades promptly. Dull or damaged blades not only compromise the quality of cuts but also put extra strain on the machine, potentially leading to more significant problems.
Hydraulic System
The hydraulic system is the powerhouse of these machines. Check the hydraulic fluid levels regularly and top up as needed. Inspect hydraulic hoses and connections for leaks and wear. Any signs of system issues should be addressed promptly to prevent performance degradation and maintain the reliability of your machine.
Electrical Systems
Ensure that all electrical components, including wiring, switches, and control panels, are in good working condition. Loose or damaged electrical connections can lead to operational disruptions and pose safety risks. Regularly inspect and maintain the electrical systems to keep your machine running smoothly. This includes checking for signs of wear, corrosion, or loose connections.
Cleanliness
A clean machine is a happy machine, and cleanliness is crucial to maintaining your Metal Shear‘s efficiency. Regularly clean the entire machine, removing dust, debris, and metal shavings that can accumulate in and around the cutting area. This improves performance, reduces the risk of fire hazards, and ensures a safer working environment.
Alignment
Proper alignment is critical for achieving precise cuts consistently. Periodically check and adjust the blade alignment to meet the required specifications. Misaligned blades can result in uneven cuts and may cause premature wear of the machine. Regular alignment checks are essential for maintaining the quality and accuracy of your steel products.
Record Keeping
Maintain comprehensive records of all maintenance activities, inspections, and repairs performed on your Metal Shear. This documentation is a valuable resource for tracking the machine’s history, identifying recurring issues, and effectively scheduling preventive maintenance. A well-organized record-keeping system helps ensure that no critical maintenance tasks are overlooked.
Preventive Maintenance Schedule
Developing a preventive maintenance schedule tailored to your specific Metal Shear model and usage is essential. Regularly consult the manufacturer’s recommendations for maintenance intervals and follow them diligently. This helps address potential problems before they become major issues, saving you time, money, and headaches in the long run.
Applications of Metal Shear
Metalworking Industry
The most common application involves cutting sheet metal in various thicknesses. From building rooftops to crafting car parts, Metal Shears cut sheet metal into desired shapes for countless applications.
HVAC Sector
These machines made accurate cuts and clean edges on sheet metals for ducts and ventilation systems.
Electronics Sector
Metal Shears cut intricate shapes from thin metal sheets for computer casings, circuit boards, and other electronic components.
Textiles and Leather Sector
Fabrics, leather, and other soft materials are efficiently cut using these machines, ensuring clean edges for garments, upholstery, and more.
Plastics and Rubber Industry
They can handle various thicknesses of plastic and rubber sheets, creating components for seals, gaskets, hoses, and other applications.
What to Consider When Choosing Metal Shear
Cutting Capacity
The cutting capacity of a Metal Shear refers to the maximum thickness and width of the material it can cut. This is one of the most crucial aspects to consider because it directly affects the types of projects you can undertake. When evaluating cutting capacity, keep in mind the typical dimensions of the materials you work with. For instance, if your rolling mill primarily deals with thick steel bars, you will need a machine that can handle substantial thickness without compromising precision. On the other hand, if you work with thinner bars, a machine with a lower cutting capacity is more cost-effective.
Material Compatibility
Different Metal Shears are designed to handle various materials, such as steel, aluminum, copper, and more. It’s essential to choose a machine compatible with the materials processed in your rolling mill. Material compatibility ensures not only longevity of the machine but also quality of the cuts. For steel rolling mills, machines specifically designed for cutting steel would be the best choice. These machines are built to withstand the hardness and toughness of steel, providing clean and accurate cuts consistently.
Precision Requirements
Precision is paramount in metal-cutting operations. The quality of your final product hinges on how accurately the material is cut. High-precision Metal Shears are equipped with advanced features that allow for fine adjustments, ensuring each cut meets the exact specifications. When considering precision requirements, assess the tolerance levels acceptable for your projects. If your rolling mill produces components that require tight tolerances, investing in a high-precision machine is crucial. Conversely, for projects with more lenient tolerances, a standard precision machine might be adequate.
Safety Features
Safety should never be compromised in any industrial setting, and Metal Shears are no exception. Modern versions come equipped with various safety features designed to protect operators and prevent accidents. Consider the machine’s compliance with industry safety standards and regulations. Ensuring the safety of your workforce protects your employees and also minimizes downtime and potential liabilities.
Ease of Operation
The ease of operation is another critical factor to consider. A user-friendly Metal Shear can significantly reduce training time and increase overall efficiency. Look for machines with intuitive controls, clear displays, and automated features that simplify the cutting process. Some advanced models offer programmable settings, allowing operators to save and recall specific cutting parameters for repeated tasks. This feature can be particularly beneficial for rolling mills that handle a variety of projects, as it streamlines the workflow and reduces the likelihood of errors.
Space and Installation Requirements
The physical space available in your facility and the installation requirements of the Metal Shear are practical considerations that can’t be overlooked. Measure the available space in your rolling mill and compare it with the dimensions of the machines you are considering. Ensure there is adequate room for installation, operation, and maintenance activities. Additionally, consider the power supply and other infrastructure requirements of the machine. Some machines may require specific electrical setups or foundations, so it’s essential to account for these needs in your planning.
FAQ
Q: What are the three main components of a Metal Shear?
Q: What is the tolerance of a Metal Shear?
Q: What are the three 3 factors that affect shearing operation?
Q: What is the clearance of a Metal Shear?
Q: How high to mount a Metal Shear?
Q: What is the rake angle of a Metal Shear?
Q: How many cutting edges does a Metal Shear have?
Q: What is the rake on a Metal Shear?
Q: What is the gap between shear blades?
Q: Is a Metal Shear used to cut flat strips?
We're well-known as one of the leading waste baler manufacturers and suppliers in China. If you're going to buy high quality waste baler made in China, welcome to get more information from our factory.