Duty Shear
Duty shears are essential tools in the recycling industry, designed to compress various types of metal scraps into compact bales. These robust machines are engineered to handle both ferrous and non-ferrous materials, streamlining the recycling process and enhancing the efficiency of scrap metal management. The versatility of hydraulic metal balers is evident in their ability to process a wide range of materials from thin iron sheets to bulky stainless steel objects. Their application is crucial in facilities like junkyards and recycling centers, where they transform diverse metal scraps, including cans, vehicle parts, and metal offcuts, into manageable bales. Constructed with durability in mind, scrap balers are typically made from high-strength steel and feature advanced hydraulic systems for powerful compression. The design of these machines allows for various methods of metal discharge, catering to the specific needs of the operation, whether it involves side-turning or forward-pushing discharge.
Advantages of Duty Shear
Precision cutting
Metal shear machines are designed to cut metal into specific sizes, making them highly useful in metal fabrication and recycling processes where exact dimensions are needed.
Versatility
These machines are equipped to work with a diverse array of metal materials, including steel, aluminum, and copper, and can manage different thicknesses and dimensions.
Time-efficient
Metal shear machines allow for quick and efficient cutting of large volumes of metal, increasing productivity in industrial settings.
Durable and robust
Metal shear machines are built to handle heavy-duty materials and processes, making them reliable in tough working conditions.
-
Hot Sale Heavy Duty Scrap Metal Hydraulic Shear BalersFeatures HBS series heavy duty steel shear, used in all kinds of thin material the production and life use scrap steel and light metal structure all kinds of plastic non-ferrous metal (stainless steel steel etc.) after the compression packaging directly cut into required sizeread more
-
Good Quality Hydraulic Waste Metal Steel Shear Baler MachineHBS Scrap baler shear machine, This equipment mainly can be used to: pre compression and shear waste.Shear reinforcement steel.Pack light.Compression, shear car bodies.Shear packer HDJ series heavy-duty hydraulic shearing machine, used for various thin material, the production and living with...read more
-
Hydraulic Heavy Duty Scrap Baling ShearOur balers have 13 series,including Y81 series hydraulic metal baling machine, Y82 series non-metal hydraulic baling machine, Y82 series scrap tire baling machine, HBS series large shearing baler,Q15 series gantry plate shears, Y32 series four-column hydraulic press, EPM series automatic waste paper baler, KSB series waste shredder and so on.read more
-
Box Shear BalerBox shearing machine is a method commonly used in scrap steel processing and production. It is widely used in the field of scrap steel processing and is one of the main methods for scrap steel processing.Compared with flame cutting, equipment shearing has the advantages of high degree of mechanization, high operation efficiency, low scrap steel loss, and no air pollution...read more
-
Automatic Horizontal Shear MachineThe fully automatic shearing machine is mainly used to cut the straight edge of metal sheets of various sizes, and is widely used in various industrial sectors such as steel rolling, automobiles, airplanes, ships, tractors, bridges, electrical appliances, instruments, boilers, etc...read more
Why Choose Us
Our factory
Our company is a professional design and manufacture company of hydraulic machinery. We are a backbone company in manufacturing all kinds of hydraulic equipment and metal machineries in domestic.
Our product
Our products have 13 series, a total of more than one hundred varieties, including Y81 series hydraulic metal baling machine, Y82 series non-metal hydraulic baling machine, Y82 series scrap tire baling machine, Y83 series hydraulic scrap metal briquetting press, HBS series large shearing baler, Q43 series crocodile hydraulic shears, Q15 series gantry plate shears, Y32 series four-column hydraulic press, EPM series automatic waste paper baler, KSB series waste shredder and so on.
Production market
Our products have been exported to more than 40 countries, such as Russia, Australia, USA, UK, Germany, Ukraine, Iran, Romania, Hungary, Mexico, Brazil, Chile, Canada, Spain, Colombia, etc. We have agents in the USA, Australia, Singapore, Kuwait, Russia.
Our certifications
Our company has been through professional quality system certification, CE certification, SGS audit and as a member of the China national resources recycling association
Working of Duty Shear
The most popular shearing machine operation, punching, is used to scrap sheared slug. Shearing also takes place between a punch and a die. Punching, Cutting, blanking, Piercing, notching, Perforating, and nibbling are all part of the shearing operation.
Punching or Blanking
Using a punch to remove material from a strip of sheet metal or a more significant piece is known as blanking or punching. Punching means removing small pieces; blanking means removing small scrap parts and the remaining helpful portion.
Cutting
Very little excess metal is spread on the parting plane during drop forging or die-casting parts production. The extra metal, referred to as flash, is removed from the part during the trimming process before it is used. Blanking and trimming are similar processes, and the dies used in each process are similar.
Piercing
Piercing is the definition of tearing a hole in metal. Because slug is not generated during piercing, it differs from punching. A drilled hole resembles a bullet hole in a metal sheet rather closely.
Nibbling
Nibbling is a particular notching where the metal is sliced with overlapping notches. Nibbling is used to create any desired shape, such as flanges or collars.
Perforating
The process of creating a uniform spacing of holes in a metal sheet that can be any size or shape and cover the entire sheet is known as this.
Making a notch
Cutting a small amount of metal from a blank is known as notching. Because the cutting line of the slug touches one edge of the strip or blank during notching, it differs from punching. Any shape can be used for notches.
What Are the Mail Applications of Duty Shear
Metal fabrication industry
Duty shears are commonly used for cutting metal sheets, steel plates, aluminum sheets, etc., for the production of automotive components, machinery parts, steel structures, etc.
Construction industry
Used for cutting and processing construction materials such as reinforcing bars, steel plates, etc., for the fabrication of building structures and components.
Automotive manufacturing
Duty shears are used for cutting automotive body panels and parts such as doors, roofs, as well as manufacturing chassis components.
Aerospace industry
Used for machining metal components of aircraft, spacecraft, as well as outer casings and structural components of aerospace vehicles.
Electronics manufacturing
Used for cutting and processing metal enclosures, metal sheets, etc., for electronic products such as phones, computers, etc.
Furniture manufacturing
Duty shears can be used for processing metal components of furniture such as tables, chairs, cabinets, etc.
Metallurgical processing industry
Duty shears are used in the cutting and shaping of metal sheets and steel during steelmaking and processing.
Agricultural machinery manufacturing
Duty shears are used for processing metal components of agricultural machinery such as harvesters, tractors, etc.
Choosing the Right Duty Shear for Your Fabrication Needs
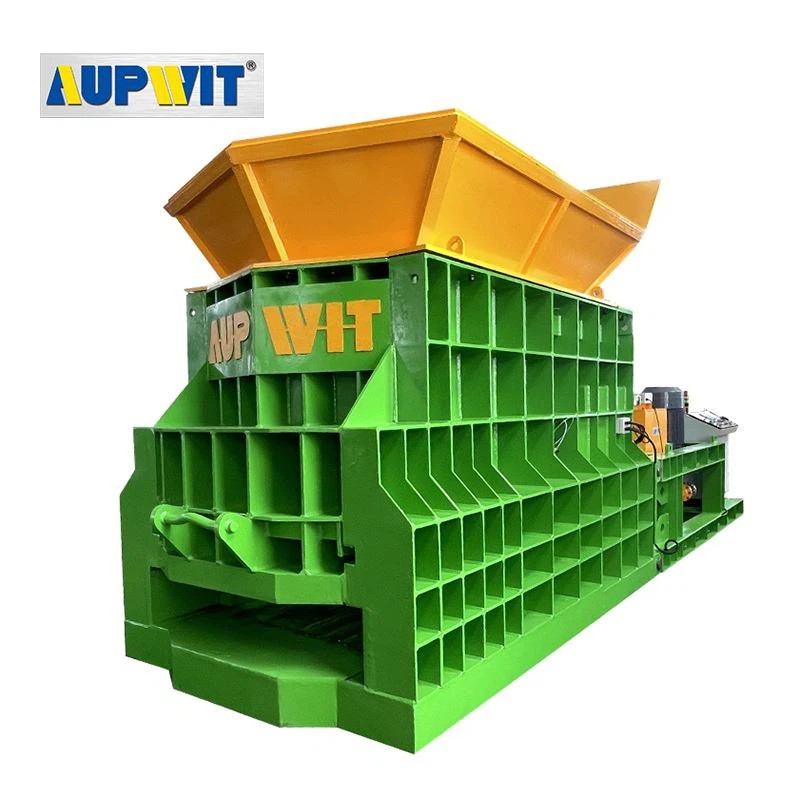
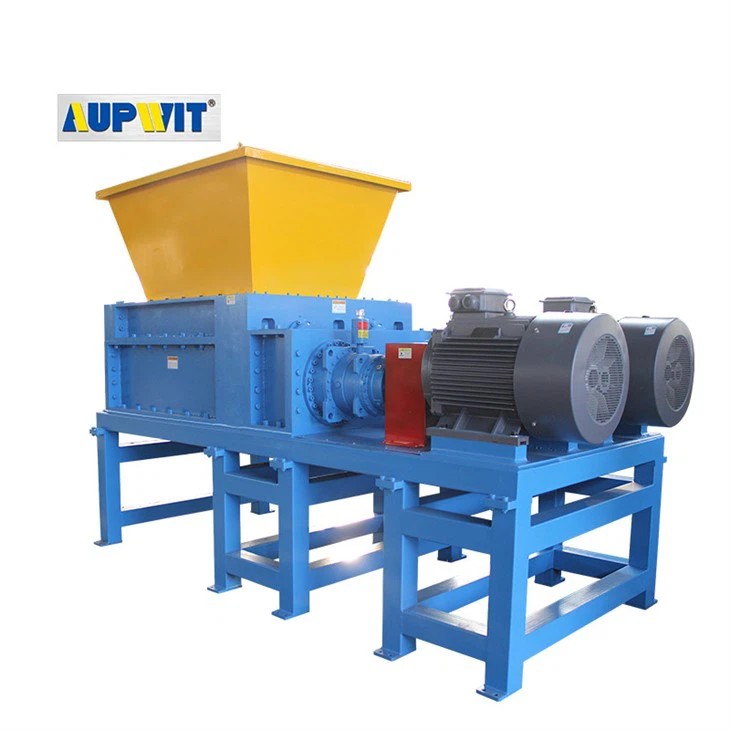
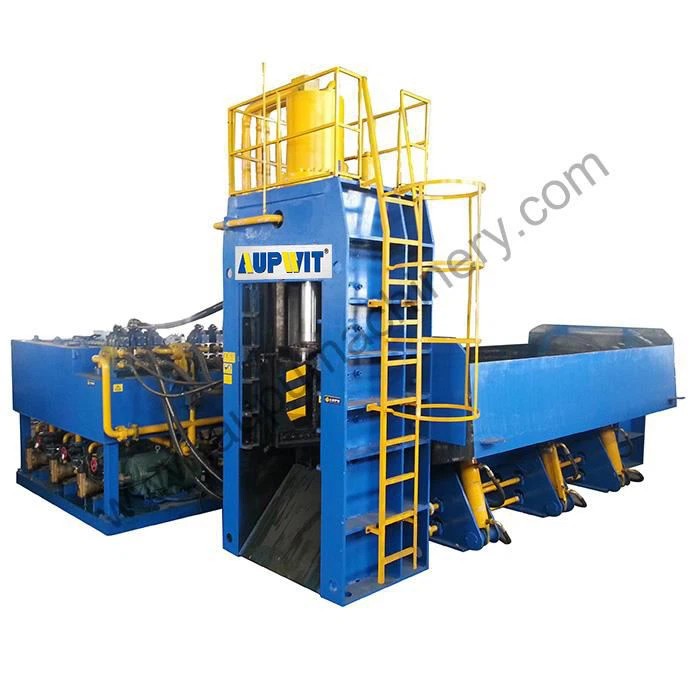
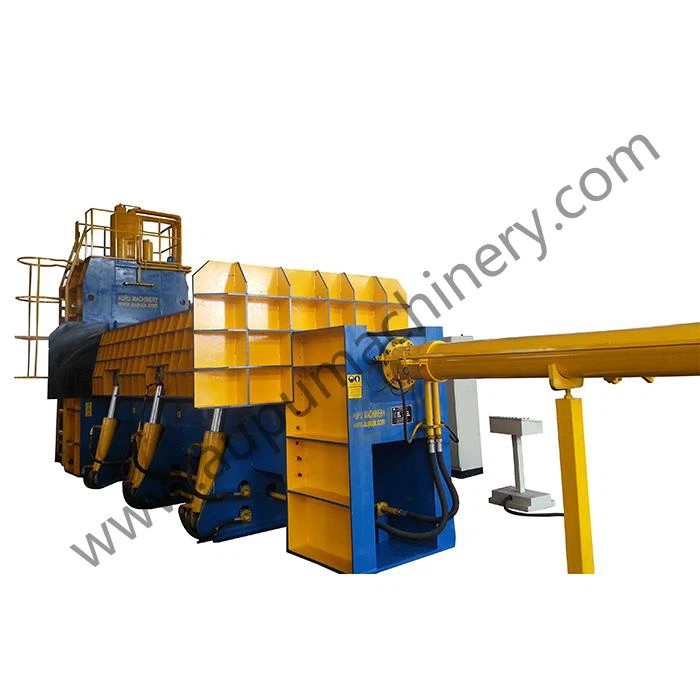
In the world of metal fabrication, precision and efficiency are paramount. Industrial shears, also known as shear machines or sheet metal shears, play a pivotal role in cutting and shaping metal sheets to meet specific design and construction requirements. However, selecting the right industrial shear for your fabrication needs can be a critical decision.
Cutting capacity and material compatibility
The first and foremost consideration when choosing duty shears is their cutting capacity and compatibility with the materials you work with. Different shear machines are designed to handle specific thicknesses and types of materials. For instance, hydraulic shears are capable of cutting thick metal sheets, while mechanical shears are better suited for thinner materials. Ensure that the shear you choose aligns with the range of materials you regularly work with to optimize efficiency and accuracy.
Shear type: Hydraulic vs. Mechanical
Industrial shears come in two primary types: Hydraulic and mechanical. Each has its advantages and is better suited to specific applications:
Hydraulic shears: These shears are known for their immense cutting power and versatility. They excel at cutting thicker materials and are ideal for heavy-duty applications. Hydraulic shears provide precise control over the cutting process and are less likely to cause material distortion.
Mechanical shears: Mechanical shears are typically more compact and cost-effective. They are suitable for cutting thinner materials and are often used for lighter-duty tasks. These shears operate with a flywheel and can be a good choice for smaller fabrication shops with less demanding cutting requirements.
Shear size and footprint
The physical size of the industrial shear is another critical factor to consider. Your available workspace and the size of the materials you work with will dictate the ideal shear size. It’s essential to ensure that the shear fits comfortably within your fabrication facility and allows for efficient material handling.
Cutting length and blade options
The cutting length of the shear, which determines the maximum width of material that can be processed, is a vital parameter. Consider the typical sizes of metal sheets or plates you work with and choose an industrial shear with an appropriate cutting length. Additionally, inquire about blade options and their availability for the shear you are considering. Different blades are designed for specific materials and cutting requirements, so having options can enhance the versatility of your shear.
Safety features and operator comfort
Safety should always be a top priority in any fabrication environment. When selecting an sheet metal shear equipment, look for built-in safety features such as blade guards, emergency stop buttons, and two-hand operation controls. These features help protect operators from potential accidents. Additionally, consider the ergonomics of the shear, as operator comfort and ease of use can contribute to overall productivity and safety.
Maintenance of Duty Shear
Daily maintenance
Before each start-up, add lubricating oil on time, at fixed points, and in fixed quantities according to the lubrication chart. The oil should be clean without sediment. The machine must be kept clean frequently, and rust-proof grease should be applied to unpainted parts.
10 minutes before getting off work every day, lubricate and clean the machine. Clean the machine every week, and add lubricating oil to each guide surface, sliding surface, ball, and lead screw.
Regular inspection
Regularly check the straightness and axial clearance of the lead screw. If it exceeds the tolerance or is too large, replace or adjust it in time. Regularly check whether the v-belt, handle, knob, and buttons are damaged. Those with severe wear should be replaced in time.
Regularly inspect and repair switches, fuses, and handles to ensure their reliable operation. The lubricating oil in the motor bearing should be replaced regularly, and check whether the electrical parts work normally.
Blade maintenance
Regularly check the wear of the blades. Dull blades should be sharpened or replaced in time. Stop the machine first when replacing the blade, and ensure that the new blade is installed securely.
Other key points
Strictly follow the operating procedures and eliminate illegal operations. Keep the working environment clean and clean up the cutting waste in time. Turn off the power when leaving the machine for a long time to prevent non-professionals from operating.
If there is any abnormality during operation, press the emergency stop button immediately and troubleshoot the cause of the fault.
What Are the Main Components of a Duty Shear
Frame
The frame provides the structural support and stability to the entire machine. It is usually made of heavy-duty steel or cast iron to handle the forces generated during the shearing process.
Bed
The bed is a flat, horizontal surface where the material to be cut is placed. It is typically equipped with scales, guides, and squaring arms to assist in precise positioning and alignment of the workpiece.
Upper and lower blades
The duty shear consists of two blades, an upper blade and a lower blade, which perform the cutting operation. The upper blade is mounted on a moving ram or beam, while the lower blade is fixed to the bed or the machine frame.
Hold-down device
The hold-down device is used to secure the workpiece firmly against the bed during the shearing process. It prevents any movement or lifting of the material, ensuring accurate cutting.
Drive system
The drive system provides the power to move the upper blade and perform the cutting action. It typically consists of an electric motor, flywheel, gears, and a clutch. The motor provides rotational power, which is transmitted to the flywheel and then converted into linear motion to move the upper blade.
Back gauge
The back gauge is an adjustable stop or fence located behind the cutting area. It helps in setting the desired cutting length by accurately positioning the workpiece before shearing.
Control panel
The control panel houses the electrical controls and switches for operating the duty shear. It allows the operator to control the cutting cycle, adjust settings, and monitor various parameters such as blade clearance, cutting length, and speed.
Safety features
Duty shears are equipped with safety features to protect the operator and prevent accidents. These may include safety guards, emergency stop buttons, foot pedals, and interlocking systems that disable the machine when accessed or opened.
Duty Shear Process Steps
Regardless of the type of duty shear used, the process generally involves the following steps: The metal sheet is placed on the machine's cutting bed, and the backgauge is set to the desired cutting length.
The hold-down mechanism is engaged to secure the metal sheet in place. The blade is lowered onto the metal sheet, applying high force to cut through the metal.
The blade is retracted, and the metal sheet is removed from the cutting bed. Duty shears are highly efficient and can cut large quantities of metal sheets quickly and accurately. However, like any machine, they require proper maintenance and safety precautions to ensure they operate effectively and safely. It's important to follow the manufacturer's instructions and guidelines when operating a duty shear to avoid accidents and damage to the machine.
Our factory
Our company has been through professional quality system certification, CE certification, SGS audit and as a member of the China national resources recycling association. Machine main core parts, use Germany Siemens motor, France Schneider electric, USA KK pressure gauge, USA parker valve, Germany Rexroth valve, Pikes high-pressure hose. Technology and performance of our products has reached the industry leading level, and has won the trust of the customers. Our company is a professional design and manufacture company of hydraulic machinery. We are a backbone company in manufacturing all kinds of hydraulic equipment and metal machineries in domestic.
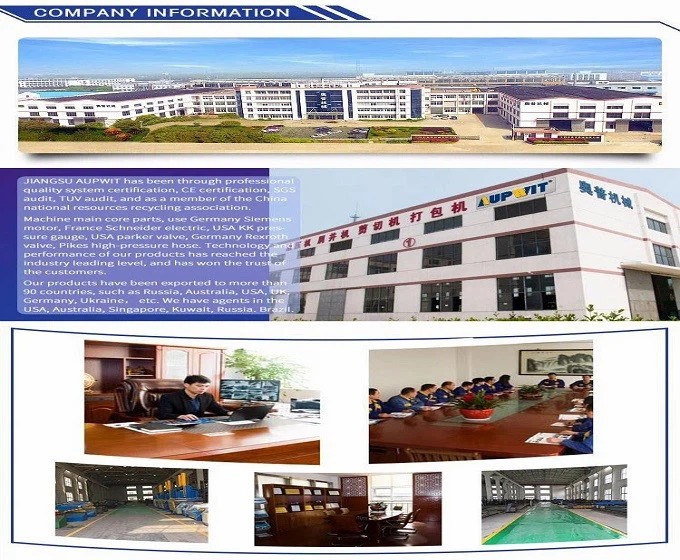
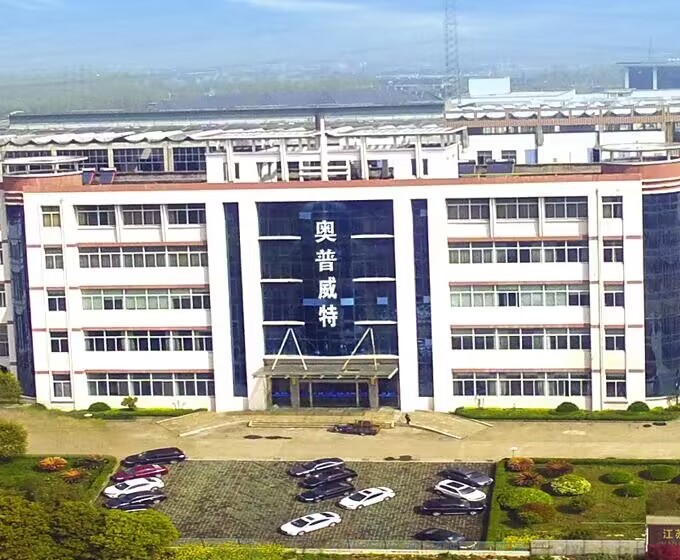
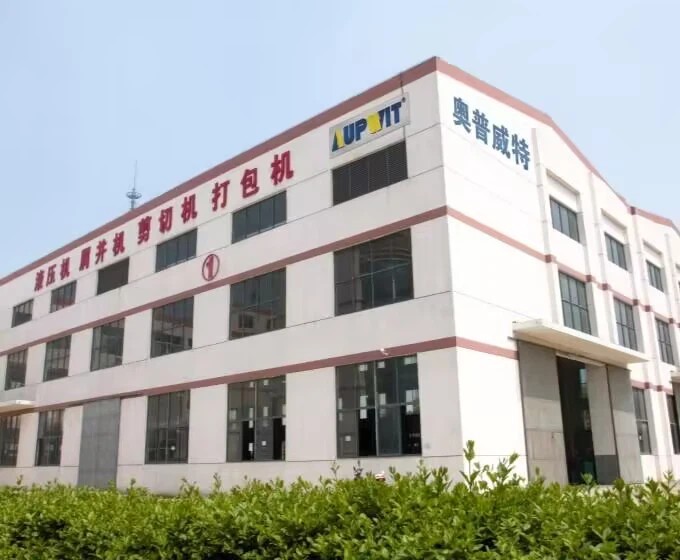
FAQ
Q: What is a duty shear?
Q: Can duty shears be automated?
Q: What is the importance of blade sharpness?
Q: How is the blade replaced on a duty shear?
Q: What is the typical lifespan of a duty shear?
Q: What are the common applications of duty shears?
Q: How do you choose the right duty shear?
Q: What is the impact of improper use of duty shears?
Q: What are the main types of duty shears?
Q: What is the difference between manual and electric duty shears?
Q: What industries commonly use duty shears?
Q: How is the cutting angle adjusted on a duty shear?
Q: What are the advantages of using a duty shear?
Q: What is the role of the hold-down mechanism?
Q: What innovations are being made in duty shear technology?
Q: What is the future of duty shears in manufacturing?
Q: How does a hydraulic duty shear work?
Q: What materials can be cut with duty shears?
Q: What is the maximum thickness of material a duty shear can cut?
Q: How do you maintain a duty shear?
We're well-known as one of the leading waste baler manufacturers and suppliers in China. If you're going to buy high quality waste baler made in China, welcome to get more information from our factory.