Guillotine Shear
Guillotine shears allow you to produce uniform and relatively burr-free sections of sheet metal or metal, which are then shaped on a press brake or bending machine. In the case of hydraulic guillotine shears, our CNC model includes an adjustable cutting angle. Motorized guillotine shears feature an impressive compact design and robust construction. Both series cut large material widths and thicknesses and are available with NC or CNC control. A manual guillotine shear rounds off our offer.
Advantages of Guillotine Shear
High accuracy
Guillotine shearing machines are designed to cut materials with high accuracy and precision, ensuring that the final product meets the required specifications.
High production capacity
Guillotine shearing machines can handle high volume of work and can be used for a wide range of applications, making them an ideal choice for industries with high production requirements.
Versatility
Guillotine shearing machines can cut a variety of materials, including steel, aluminum, copper, and brass. They can also cut materials of various thicknesses and sizes.
Cost-effective
Guillotine shearing machines are relatively affordable compared to other cutting machines, making them a cost-effective option for businesses that need to cut and shape metal sheets regularly.
Low maintenance
Guillotine shearing machines are generally easy to maintain and require minimal maintenance, reducing downtime and increasing productivity.
Ease of use
Guillotine shearing machines are simple to operate and require minimal training, making them a good option for small and medium-sized businesses.
-
High Pressure Hydraulic Scrap Metal Plate guillotine Shearing MachineHydraulic Scrap Metal Plate Guillotine Shearing Machine is a type of equipment used for cutting and processing scrap metal plates. It is widely used in the metal recycling industry and can be used to process various types of metal plates, such as steel plates, aluminum plates, copper plates, and so on...read more
-
Hot Sale Scrap Metal Guillotine Shear MachineQ43 series Corcodile shear machine This machine is used for a variety of cross-section shapes such as round steel, square steel, Angle steel, i-steel, plate steel, steel pipe, such as waste of cold shear, hot rolled small scale cut steel, steel rolling mills scale cutting, etc The properties and...read more
-
Hydraulic Heavy-Duty Shear for factory direct saleMetal Shear, Metal Baler, Scrap Metal Baler manufacturer / supplier in China, offering Hydraulic Heavy-Duty Scrap Baling Shear and so on.read more
-
Heavy-Duty scrap hydraulic shearing machineBaling Shear, Shear Baler, Shear manufacturer / supplier in China, offering Heavy-Duty Scrap Shears, Waste Paper Vertical Baler, and so on.Scrap recycling machine, to smelting, you can have many choices here.10 years manufacture experience.read more
-
Guillotine Shear for metal materials cuttingShears, Guillotine Shears, Hydraulic Shears manufacturer / supplier in China, offering Hydraulic Guillotine Shears Machine, CNC / Nc, Hydraulic Shearing Cutting Machine, Plate Shearing Machine, Hydraulic Swing Beam Shearing Machine, Hydraulic Swing Beam Shearing Machine and so on.read more
-
Automatic Gantry ShearQ91Y Series Automatic Gantry Shear For all kinds of production and life use scrap non-ferrous metal (stainless steel, copper, etc.) directly cut into the required size.read more
Why Choose Us
Our factory
Our company is a professional design and manufacture company of hydraulic machinery. We are a backbone company in manufacturing all kinds of hydraulic equipment and metal machineries in domestic.
Our product
Our products have 13 series, a total of more than one hundred varieties, including Y81 series hydraulic metal baling machine, Y82 series non-metal hydraulic baling machine, Y82 series scrap tire baling machine, Y83 series hydraulic scrap metal briquetting press, HBS series large shearing baler, Q43 series crocodile hydraulic shears, Q15 series gantry plate shears, Y32 series four-column hydraulic press, EPM series automatic waste paper baler, KSB series waste shredder and so on.
Production market
Our products have been exported to more than 40 countries, such as Russia, Australia, USA, UK, Germany, Ukraine, Iran, Romania, Hungary, Mexico, Brazil, Chile, Canada, Spain, Colombia, etc. We have agents in the USA, Australia, Singapore, Kuwait, Russia.
Our certifications
Our company has been through professional quality system certification, CE certification, SGS audit and as a member of the China national resources recycling association.
Types of Guillotine Shearing Machines
There are several types of guillotine shearing machines, and the choice of machine depends on the requirements of the specific application. Some of the common types of guillotine shearing machines are
Mechanical Shearing Machines
Mechanical shearing machines are powered by a motor and gears that operate the moving blade. These machines are less expensive than hydraulic shearing machines, and they are ideal for low-volume cutting.
CNC Shearing Machines
CNC shearing machines are computer-controlled machines that offer precise and repeatable cuts. These machines are ideal for high-volume cutting and for cutting complex shapes.
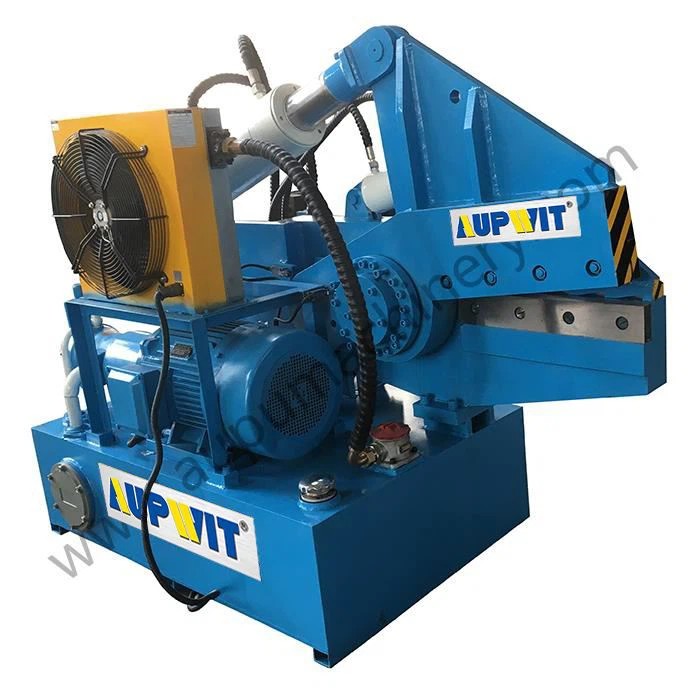
Hydraulic Shearing Machines
Hydraulic shearing machines use a hydraulic system to power the moving blade. These machines are more expensive than mechanical shearing machines, but they offer more power and precision. They are ideal for high-volume cutting and for cutting thicker sheets of metal.
Variable Rake Shearing Machines
Variable rake shearing machines allow the angle of the moving blade to be adjusted to optimize the cutting performance. These machines are ideal for cutting thicker sheets of metal and for cutting materials that are difficult to cut.
How the Guillotine Shear Works
As we have already mentioned in previous articles about the processing of sheet metal, the traditional technique for cutting sheet metal is shearing. Shearing, as the name suggests, is performed by machines called shears. The most widely used shears can be classified into two different types: guillotine and circular blades. In both cases the cutting of the sheet metal is produced by the mechanical action of two blades whose stress exceeds the resistance determining the breaking of the material.
Guillotine shears are the most common and also the most requested on the used machinery market. The guillotine shear is structurally composed by two blades, a lower fixed blade and an upper blade, movable by hydraulic pistons fed by a hydraulic unit (hydraulic compressor). All the shears are provided with a device called blank holder, this allows the clamping of the material during the cutting phase, and by adjustable guides on which the sheet slides.
The guillotine shears can have very different characteristics, with blade length up to 6 m and cutting capacity up to 20-30 mm sheet thickness. Usually, especially in large shears, the upper blade is not perfectly straight but is slightly curved or tilted longitudinally. These measures are designed to reduce the cutting effort by exploiting the scissor effect.
The scissor effect indicates a blanking that does not occur simultaneously along the entire cutting line, but works the sheet progressively, just like the scissors cutting a sheet of paper, thus avoiding excessive pressure.
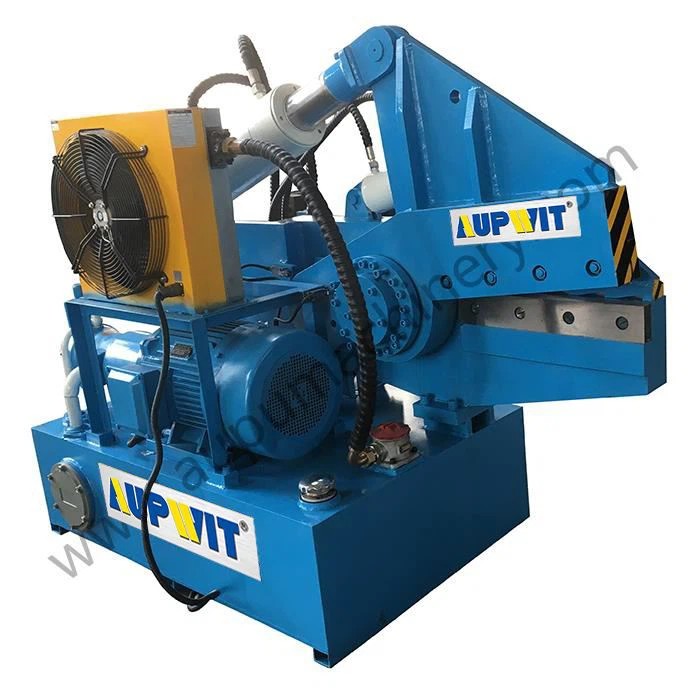
How Do the Guillotine Shear Power the Cutting Action?
Before we get to the action, so to speak, we need to understand the methods by which the machines produce the force required to move the blades. Typically, guillotines use mechanical, pneumatic, servo motor or hydraulic systems. In a motorised system, an electric motor can drive a flywheel and rolling key arrangement, or provide direct drive using a gearbox and eccentric system. The latter is preferable, as it does not require the motor to be running constantly, and only starts the motor when the pedal is pressed to initiate a cut. In the case of servo motors the machine drives the movement of the top blade with powerful electric servo motors and a set of pulleys. These modern machines are known as e-shears and are very energy efficient and quiet, but initial cost is still high. Pneumatics and hydraulics are very similar to each other, in principle. By far the most popular method is hydraulic type machines, using a motor, pump, valve set, pistons and hydraulic oil to provide a relatively efficient and very powerful force to the blades.
Swing Beam Shear Vs Guillotine Shear
Blade Cutting Edge
Guillotine shear: 4 Cutting edges for upper blade and 4 cutting edges for bottom blade.
Swing beam shear: 2 Cutting edges for upper blade and 4 cutting edges for bottom blade.
Cutting Method
Guillotine shear: Upper blade moves up and down uprightly and bottom blade is fixed on the worktable.
Swing beam shear: Upper blade moves in arc motion and bottom blade is fixed on the worktable.
Blade Gap Adjustment
Guillotine shear: Blade gap can be set by motor.
Swing beam shear: Blade gap can only be set by manual crank.
Cutting Angle Adjustment
Guillotine shear: Cutting angle cut be set step by step on controller.
Swing beam shear: Cutting angle adjustment is unavailable.
What Factors Should Be Considered When Choosing AGuillotine Shear For A Specific Application?
The premium hydraulic guillotine shearing machine is a powerful tool used for shearing materials in various industries including metal fabrication, automotive and construction. Selecting the proper hydraulic guillotine shear for a specific application is critical to ensuring optimum performance and efficiency. In this article, we discuss the factors that should be considered when selecting a hydraulic shear for a specific application.
Material type and thickness
The first factors to consider when choosing a hydraulic guillotine shear are the material type and thickness. The maximum cutting capacity of the machine should be determined to ensure it can handle the material being cut. The tonnage of the machine should also be considered to ensure it is suitable for the thickness of the material. Hydraulic shears with insufficient tonnage will result in poor cut quality and reduced efficiency.
Cutting length
When selecting a high-quality hydraulic guillotine shearing machine, the desired cutting length for the application should be determined. The cutting length of the machine should be sufficient to handle the material being processed. Choosing a machine with too small a cutting length will require multiple cuts, reducing efficiency and increasing production time.
Blade quality and type
The type and quality of blades used in a hydraulic guillotine shearing machine can significantly affect shear quality and efficiency. It is crucial to understand the different types of blades available and choose the right one based on the type of material and desired cut quality. A hydraulic guillotine shear with the wrong blade type or quality will result in poor cut quality, reduced efficiency and increased maintenance costs.
Control system
The control system of a quality hydraulic guillotine shearing machine is another key factor to consider when selecting a machine for a particular application. Understanding the different types of control systems available and selecting the one that meets the needs of the application can significantly impact efficiency and productivity. A control system that is difficult to use or does not meet the needs of the application can result in reduced efficiency and productivity.
Security features
Safety is a top priority when using hydraulic guillotine shears. A machine with appropriate safety features must be selected for a particular application. Safety features such as guards, emergency stop buttons and safety interlocks prevent accidents and injuries in the workplace. Choosing a machine with insufficient safety features can result in accidents, injury and increased liability.
Budget and ROI
The budget for purchasing a hydraulic guillotine shear and the expected return on investment (ROI) should be considered when selecting a machine for a specific application. Selecting a machine that exceeds budget or does not provide an adequate return on investment can result in reduced profitability and increased financial risk.
How to Properly Maintain and Care for a Guillotine Shear to Ensure Optimal Performance and Longevity?
Clean and lubricate
Keeping your guillotine shear for metal clean and well lubricated is fundamental to proper maintenance. Regular cleaning prevents the accumulation of dust, metal shavings and debris that can affect the machine’s performance. Additionally, lubricating moving parts and assemblies helps reduce friction and prevent premature wear.
To clean the scissors, first disconnect the machine from the power source. Use a brush or compressed air to remove any accumulated debris. Pay special attention to the cutting area, backgauge system and guide rails. After cleaning, apply the recommended lubricant to the pivot points, guides, and ball screws according to the manufacturer’s guidelines.
Inspection and fastening of components
Frequent inspections are critical to early detection and resolution of potential problems. Regularly inspect critical and moving parts for signs of wear, damage, or misalignment. Check the blade for any chipping or dulling, as a sharp blade is essential for a clean cut and longer machine life.
Tighten loose parts in time to prevent further damage and ensure smooth operation of the machine. Note the backgauge system, hydraulic connections, and mechanical components. Refer to your machine manual for the correct torque value when tightening fasteners.
Blade maintenance and sharpening
The blade is at the heart of any guillotine shear and maintaining its sharpness is critical for optimum performance. A dull blade not only affects cut quality, but also puts extra stress on the machine, causing premature wear.
Sharpen the blades regularly or replace them when necessary. Depending on the purpose and material type of the scissors, the frequency of sharpening may vary. When sharpening your blades, make sure they are balanced and aligned correctly to avoid problems during cutting.
Check hydraulic oil level
The hydraulic system plays a key role in the operation of the hydraulic guillotine shearing machine. To ensure smooth operation, proper hydraulic fluid levels must be maintained. Check the hydraulic oil tank regularly and make sure it is filled to the recommended level. Low fluid levels can lead to poor hydraulic system performance or even damage.
Replace the filter
Filters are a critical component in keeping hydraulic systems clean and free of contaminants. Inspect and replace filters regularly according to the manufacturer’s guidelines. Clogged or dirty filters can reduce the efficiency of the hydraulic system and cause excessive wear on components.
Hydraulic system inspection
Check the hydraulic system regularly for signs of leaks, hose or fitting damage. Leaks can cause a drop in hydraulic pressure and significantly affect the cutting ability of the shear. Address any hydraulic system issues promptly to avoid costly repairs and potential downtime.
Check electrical connections
The electrical system in the hydraulic guillotine shear for metal is responsible for controlling various functions. Regularly inspect electrical connections for signs of wear, damage, or looseness. Connection errors can cause operational problems and pose security risks.
Control panel maintenance
The control panel is the interface for the operator to control the functions of the shear. Keeping your control panel clean and protected is critical to ensuring its longevity. Avoid exposure to water, dust, or excessive heat, which may damage electronic equipment. Also, update software and firmware according to the manufacturer’s recommendations to get the latest features and improvements.
Lockout/tagout procedures
Safety should always be the top priority when performing maintenance tasks. Before starting any maintenance or inspection, make sure the hydraulic gate shear is turned off and disconnect it from power. Implement lockout/tagout procedures to prevent accidental activation, which could result in serious injury.
Personal Protective Equipment (PPE)
Wearing the proper personal protective equipment (PPE) is essential to keep maintenance personnel safe. Depending on the task involved, operators should wear safety glasses, hearing protection, gloves, and other necessary personal protective equipment to protect against potential hazards.
Our factory
Our company has been through professional quality system certification, CE certification, SGS audit and as a member of the China national resources recycling association. Machine main core parts, use Germany Siemens motor, France Schneider electric, USA KK pressure gauge, USA parker valve, Germany Rexroth valve, Pikes high-pressure hose. Technology and performance of our products has reached the industry leading level, and has won the trust of the customers. Our company is a professional design and manufacture company of hydraulic machinery. We are a backbone company in manufacturing all kinds of hydraulic equipment and metal machineries in domestic.
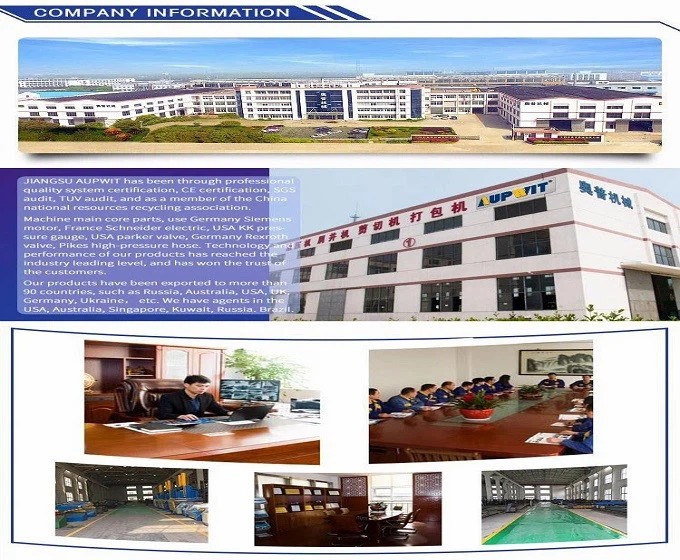
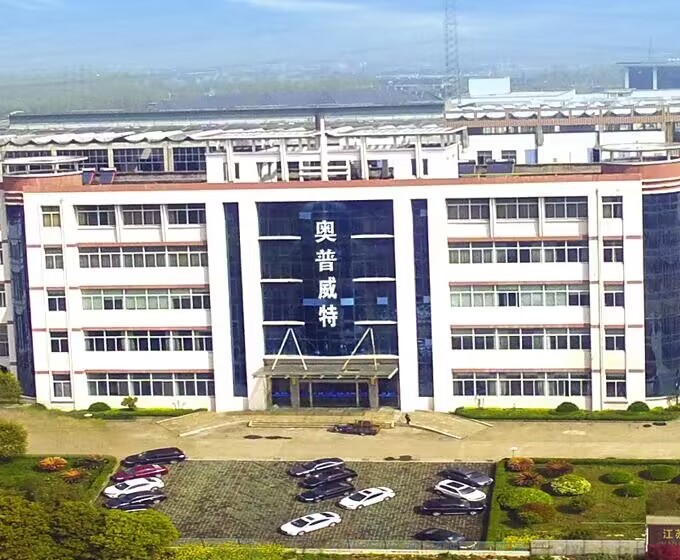
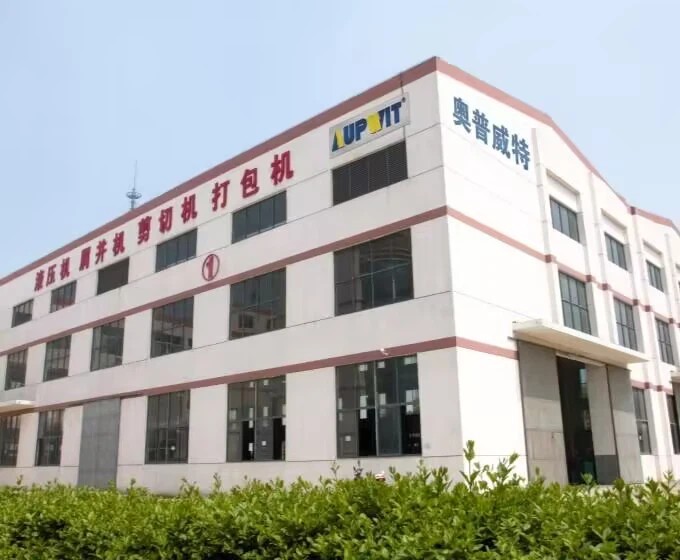
FAQ
Q: What is a guillotine shear?
Q: How does a guillotine shear work?
Q: What is the lifespan of a guillotine shear?
Q: Can guillotine shears be used for curved cuts?
Q: What industries commonly use guillotine shears?
Q: What is the role of the hold-down mechanism?
Q: How do you choose the right guillotine shear?
Q: What is the importance of blade sharpness?
Q: How is the blade replaced on a guillotine shear?
Q: What is the maximum sheet size a guillotine shear can handle?
Q: What training is required to operate a guillotine shear?
Q: What are the common applications of guillotine shears?
Q: What is the future of guillotine shears in manufacturing?
Q: What materials can be cut with a guillotine shear?
Q: What are the main components of a guillotine shear?
Q: What are the advantages of using a guillotine shear?
Q: What is the typical cutting capacity of a guillotine shear?
Q: How is the cutting angle adjusted on a guillotine shear?
Q: What safety features should a guillotine shear have?
Q: How do you maintain a guillotine shear?
We're well-known as one of the leading waste baler manufacturers and suppliers in China. If you're going to buy high quality waste baler made in China, welcome to get more information from our factory.