Briquetting Press
Jiangyin Aupu Machinery Co.,Ltd.:Your Trustworthy Briquetting Press Manufacturer!
Our company is a professional design and manufacture company of hydraulic machinery. We are a backbone company in manufacturing all kinds of hydraulic equipment and metal machineries in domestic. Our company has been through professional quality system certification, CE certification, SGS audit and as a member of the China national resources recycling association.
Leading Service
We are committed to constantly innovating our products to provide foreign customers with a large number of high-quality products to exceed customer satisfaction. We can also provide customized services according to customers' requirements such as size, color, appearance, etc. We can provide the most favorable price and high-quality products.
Quality Guaranteed
We have been continuously researching and innovating to meet the needs of different customers. At the same time, we always adhere to strict quality control to ensure that the quality of every product meets international standards.
Wide Sales Countries
Our products have been exported to more than 40 countries, such as Russia, Australia, USA, UK, Germany, Ukraine, Iran, Romania, Hungary, Mexico, Brazil, Chile, Canada, Spain, Colombia, etc. We have agents in the USA, Australia, Singapore, Kuwait, Russia.
Various Types of Products
Our products have 13 series, a total of more than one hundred varieties, including Y81 series hydraulic metal baling machine, Y82 series non-metal hydraulic baling machine, Y82 series scrap tire baling machine, Y83 series hydraulic scrap briquetting press, HBS series large shearing baler, Q43 series crocodile hydraulic shears, Q15 series gantry plate shears, Y32 series four-column hydraulic press, EPM series automatic waste paper baler, KSB series waste shredder and so on.
-
Metal Briquetting MachineMetal briquetting machines are an essential tool for the metal recycling industry. They enable metal scraps to be compressed into compact briquettes, making it easier to transport and store these materials. This innovative machine is widely used in various metalworking processes, including automotive, aerospace, and manufacturing industries...read more
-
Metal Briquetting Machine Production LineY83 Series Metal Chips Briquetting Press Line can replace the traditional dual steps of drying and briquetting, the metal chips with a large amount of coolant after mechanically processed are compressed into dry blocks through this briquetting machine in one step, and the contained coolant is recovered at the same time for recycling and reuse...read more
-
Briquetting Presses for Metal ChipsThe Y85 Double-end Metal Chips Briquetting Machine is a real all-rounder and is suitable for pressing aluminium, steel, cast iron, copper and countless other metals. The briquette press compacts metal chips and swarf into near solids cylindrical briquettes that can be efficiently remelted increasing the value of your scrap. During the briquetting process, residual fluid is removed due to the intense pressure exerted on the chips and is collected into a containment tray...read more
A briquetting press is used to turn the waste fine/powder into a regular shape block, which can help to improve the physical or chemical conditions for those powder, make it easy for transportation, storage, reduce the generated dust and be more useful for further applications. The briquette system is able to deal with all kinds of materials under suitable sizes and moisture. Briquetting work always takes place with the binder as the raw particles need the binding effect to get enough strength when they are turned to briquette, whatever it’s internal or extra additives. Biomass and industrial waste are sometimes different from each other when briquetting due to the binder source they are using.
Benefits of Briquetting Press
Safe and Efficient
The feeding mode of the briquetting press is that the metal chips are automatically lifted and turned to the feeding port by the hoist to ensure the safe operation of the equipment. It is equipped with an independent hydraulic system and designed hydraulic automatic feeding device to achieve automatic production and ensure efficient operation and personnel safety.
Intelligent Control
The whole chip processing production line adopts touch screen automation control. It has the functions of counting the compressed finished products, oil temperature alarm, fault recording and early warning. The running parameters can be set easily, presented in real time, monitored and recorded.
Stable and Reliable
The briquetting press, a core equipment, is equipped with planetary reducers and products of other brands to ensure the long-term stable operation of the equipment. The chip waferer adopts the advanced hydraulic system design with intelligent cooling and constant temperature of hydraulic oil to ensure the continuous and stable operation of the system.
Energy Saving and Environmental Protection
Metal chips are transported from feeding to the completion of pressing in a closed environment to avoid leakage of liquid and chips. The waste liquid squeezed out flows to the purification and collection box for filtration and recovery. When the chip liquid reaches the level scale, it is automatically pumped to avoid secondary pollution.
Space-saving
Horizontal metal chip briquetting presses typically require less vertical space than vertical briquetting presses. This makes them suitable for facilities with limited height.
Uniform Briquettes
The machine produces uniform briquettes with consistent density and size. This uniformity is essential for efficient storage, handling, and further processing or transportation.
Versatile application
The briquetting press can process a wide range of metal scraps, including steel, aluminum, copper, and more, making it suitable for various industries such as automotive, manufacturing, and metal fabrication.
Types of Briquetting Press
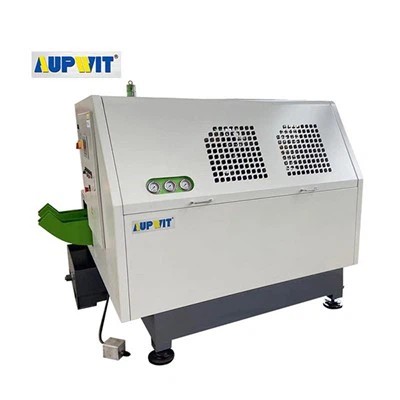
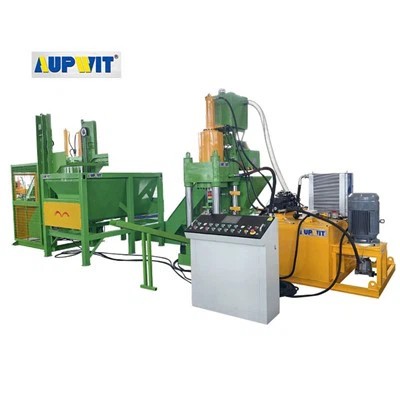
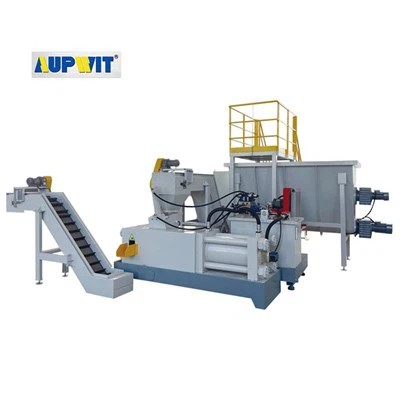
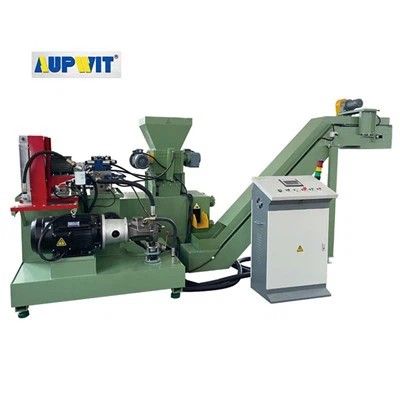
Piston Press
This briquetting press is made up of a ram (piston) and a die. It is powered by either an electric motor or a diesel engine. To make biomass briquettes with a briquetting press, a ram with a very high compaction pressure is reciprocated into a die to form a briquette. For large-scale production, the machine generates a compressive force of 200 MPa, with production ranging from almost 200 kg/h to 2,500 kg/h.
Hydraulic Press
The raw material is conveyed to the pre-compactor by the screw conveyor in a hydraulic briquetting press, after which it is pushed into the die by the main piston, which compresses the raw material into the final form. The pressure of the die in this type of briquette press can be modified, which changes the density of the final briquettes.
Manual Press
There are numerous varieties of manual briquette presses that aid in the densification of materials. These presses are operated with bare hands and rarely use electricity. They have an entirely manual operation, produce a little amount of briquettes, and are usually utilised in the home.
Screw press
Screw Briquette presses usually include three types: conical screw presses, cylindrical screw presses with heated dies, and cylindrical screw presses. In these presses, continuous feeding into a screw with heated dies to push the material into a cylindrical die to make lignin flow is used. This technology works with a special screw pressure that pushes raw material into a chamber to narrow it.
Roller Press
The roller briquette press is set up to make pillow-shaped briquettes from a variety of feedstocks. With dual cylindrical rollers rotating in opposite directions on parallel axes, it works on pressure and agglomeration. There are two rollers in the procedure to keep a tiny gap between them. It is usually determined by elements such as feedstock type, moisture content, particle size, binder addition, etc.
How Does A Briquetting Press Work?
The typical process of using a briquetting press involves the following steps
Collection of Metal Waste
Metal scraps, chips, or shavings are collected from various sources, such as machining shops, metalworking industries, and manufacturing units.
Feeding
The metal waste is fed into the briquetting press’s hopper or chamber. Some machines may require pre-processing to remove contaminants or cool down the metal before feeding it into the machine.
Compression
The metal waste is compressed under high pressure by a hydraulic or mechanical mechanism inside the briquetting press. This pressure forces the metal particles to bind together and form compact briquettes.
Ejection
Once the briquettes are formed, they are ejected from the machine through a discharge chute or conveyor belt.
Cooling and Storage
Depending on the specific material and application, the briquettes may need to be cooled before storage or transportation.
How to Maintain Briquetting Press
When disassembling the filler cap, filter cap, inspection hole, hydraulic tubing and other parts of the hydraulic oil tank of the briquetting press, avoid dust when the system oil passage is exposed. The disassembled part must be thoroughly cleaned before opening. For example, when removing the hydraulic oil tank filler cap, first remove the dirt around the fuel tank cap, unscrew the fuel tank cap, and remove the debris remaining in the joint (not flush with water to prevent water from infiltrating the fuel tank), and then open the fuel tank cap after cleaning.
If you need to use a wiping material and a hammer, you should choose a wiping material that does not remove fiber impurities and a special hammer with rubber attached to the striking surface. Hydraulic components and hydraulic hoses should be carefully cleaned and assembled after drying with high-pressure air. Use a well-packed filter element (the inner packaging is damaged, although the filter element is intact, it may be unclean). Clean the filter at the same time when changing the oil. Before installing the filter element, use the wipe material to carefully clean the bottom dirt in the filter housing.
Pay attention to the sound of the hydraulic pump and the overflow valve during the operation of the briquetting press. If the cavitation noise of the hydraulic pump can not be eliminated after exhausting, it should be used after finding the cause and troubleshooting. If an actuator moves slowly when there is no load, accompanied by the sound of overflow valve overflow, it should be shut down immediately for maintenance.
Regular maintenance of the briquetting press is required. Check the attachments on the filter screen. For example, excessive metal powder often indicates the wear of the oil pump or the pulling of the oil cylinder. For this, it is necessary to diagnose and take corresponding measures before starting the machine. If the filter screen is damaged or dirt accumulated, it should be replaced in time, and the oil should be changed at the same time if necessary.
What to Consider When Choosing Briquetting Press
Material Type: Determine the type of material or biomass that needs to be processed into briquettes. Different briquetting presses are designed to handle specific materials such as wood chips, sawdust, agricultural residues, coal, charcoal, metal chips, or biomass. Ensure that the machine you choose is suitable for the material you intend to process.
Capacity Requirements: Assess the desired production capacity in terms of the amount of material to be processed and the output of briquettes per hour or day. Choose a machine with the appropriate capacity to meet your production goals. Consider factors such as the size and frequency of the material feed, as well as the required density and size of the briquettes.
Briquette Size and Shape: Determine the desired size and shape of the briquettes. Different machines offer various options in terms of briquette dimensions and shapes. Consider whether the machine can produce the specific briquette size and shape required for your application.
Energy Efficiency: Evaluate the energy efficiency of the briquetting press. Look for machines that offer high energy efficiency to minimize operating costs and reduce environmental impact.
Automation and Control: Consider the level of automation and control features offered by the machine. Some machines have advanced automation and control systems that enable precise monitoring and adjustment of parameters such as pressure, temperature, and briquette density. Automation can improve efficiency and consistency in briquette production.
Maintenance and Durability: Assess the maintenance requirements and durability of the machine. Look for machines that are built with high-quality materials and components to ensure long-term reliability and minimal downtime. Consider the availability of spare parts and the manufacturer's reputation for after-sales support.
Budget and Cost Considerations: Determine your budget and compare the costs of different briquetting presses. Consider not only the initial purchase price but also the operational costs, including electricity consumption, maintenance, and potential costs for consumables like binders or additives. Ensure that the machine provides good value for the investment.
Safety Features: Pay attention to safety features and compliance with safety standards. Look for machines with safety guards, emergency stop buttons, and other safety measures to protect operators and prevent accidents.
FAQ
Q: What is the working principle of briquetting press?
Q: How does a briquette press work?
Q: What are the parameters of briquetting press?
Q: How much pressure is required to make briquettes?
Q: What are the components of a briquetting press?
Q: What is the process of briquetting?
Q: What are the factors affecting briquetting?
Q: What are the classification of briquetting presses?
Q: What are the components of briquetting press?
Q: What are two types of briquetting presses?
Screw press briquette makers: These tools compress the raw material and binder into a briquette using a screw.
We're well-known as one of the leading waste baler manufacturers and suppliers in China. If you're going to buy high quality waste baler made in China, welcome to get more information from our factory.